MESH-PARTICLE MULTIPHYSICS
meeting highest demands for complexity, accuracy and validity in the simplest possible way.
Combining the Best of Both Worlds
To Create Something Even More Powerful
A Unified Interface Capable of Handling
Explore a Large Variety of Materials
To Tailor Your Model
Explore A Vast Amount of Combinations
To Combine More Physics in One Single Software
Run On World‘s Fastest Chips
Solvers Architectured For Today‘s Cutting Edge
8 CPU
32 CPU
120 CPU
Today, engineers work with a wide spread of low and mid quality hardware.
GPU A100
All Dive Users
GPU H100
Beta Phase
GPU B200
Test Phase
All Dive users access only the latest and fastest HPC resources.
... and they update right after the next generation is available.
Simulation Speedup
Always Faster Than Your Competition
Legacy software needs to run on multiple platforms, old and new. Thus, never really optimized for any of those.
In the cloud-native CAE, we choose the best suitable hardware for you.
32
18
11
1
Speed Up
Development Principles
To Model Reality
Speed is essential, but enterprise-grade simulation demands accuracy above all, at scale and in the cloud
We prioritize physical accuracy, backed by a continuously growing validation suite of 100+ industrial and academic benchmarks. Complex designs impose high demands on simulation fidelity, which we meet by building models that capture key physical phenomena while preserving geometric precision. This level of detail comes at a computational cost, which we handle efficiently in parallel with modern cloud compute hardware accelerators.
Precision
Speed
Fitting past results is easy. Predicting the future requires physically grounded simulations.
We don’t rely on data calibration – we model reality. While solver parameter tuning may match individual measurements, it rarely generalizes across varying operating conditions. Our solver operates solely with physical input parameters, staying true to the fundamental laws of physics. This foundation allows us to simulate complex systems reliably for all design spaces.
Physicality
Adjustability
We build methods that preserve what nature preserves – mass, momentum and energy.
Many commercial solvers aim for higher-order schemes that neglect basic conservation principles . These may perform well in low-complexity academic benchmarks but often break down in industrial-grade applications. We develop numerical methods that strongly conserve mass, momentum and energy to ensure physically meaningful results, even in the most complex simulations.
Conservation
Consistency
Our one-solver architecture combines mesh and particle methods into a unified, end-to-end simulation environment.
We customize every part of the workflow to perfectly fit our solver. Tailored preprocessing handles complex geometries with high accuracy, and postprocessing reflects the solver’s internal logic to ensure consistent and reliable results. This close integration avoids fragile combinations of separate tools and methods, making the entire simulation setup easier, more automated, and less error-prone.
Unification
Fragmentation
Built-In Features
To Focus On Just Engineering
Preprocessing
Solver
Postprocessing
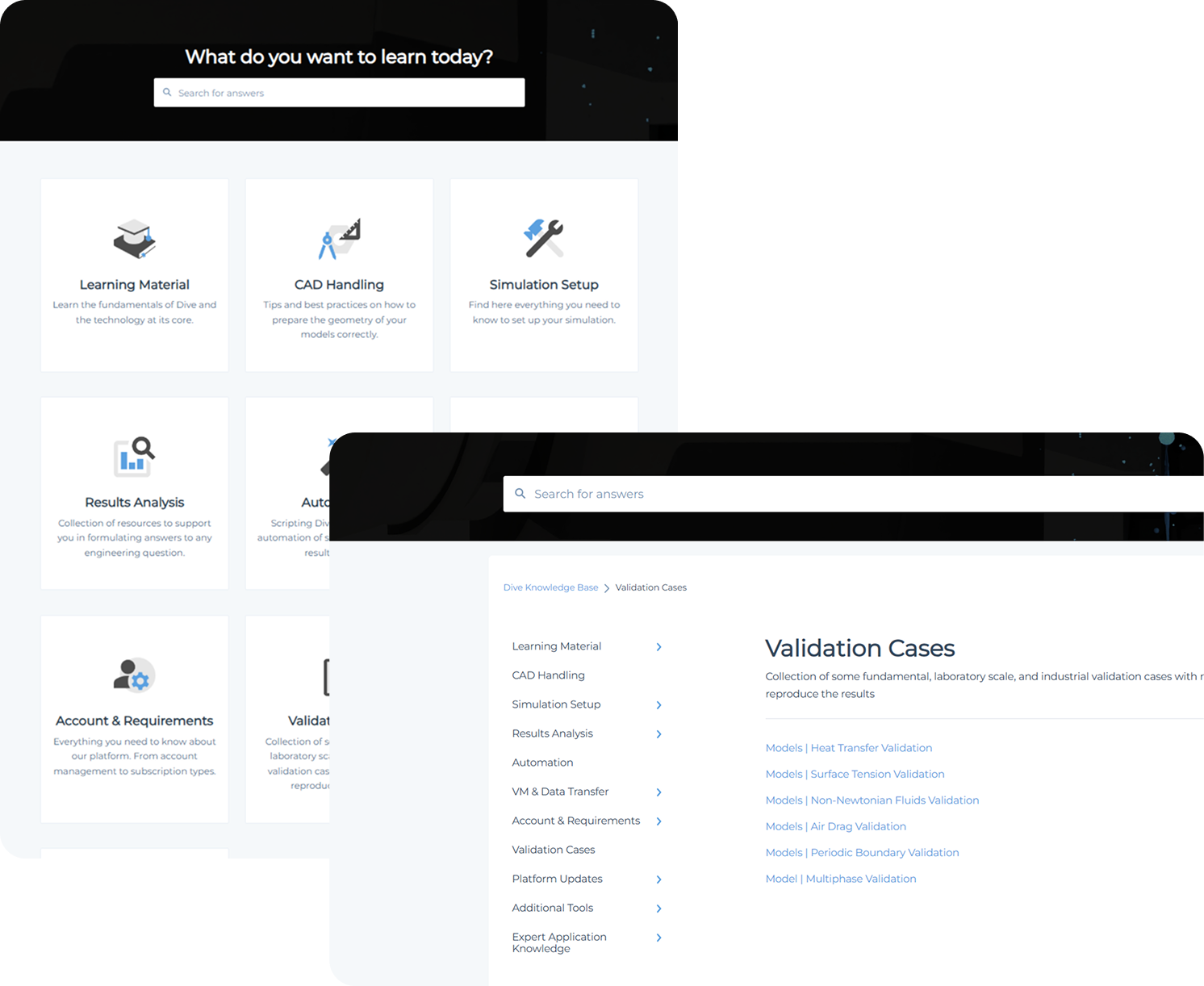