Many processing lines run with conservative cycle times or excessive input, “just to be safe.” This leads to wasted utilities, and overprocessing.
Dive enables engineers to observe the flow, heat transfer, and material behavior inside equipment inreal-time - optimizing heating, mixing, and cleaning durations.
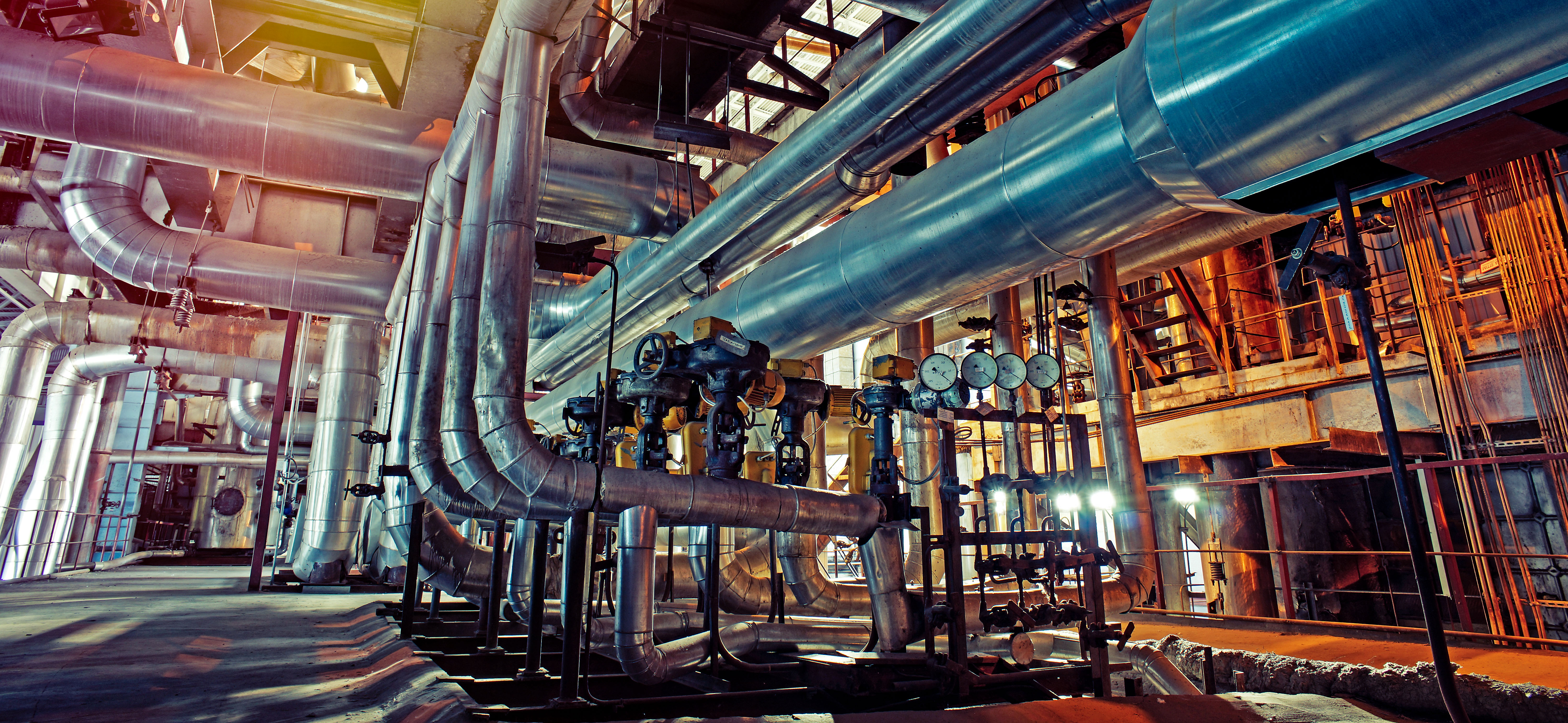