Electric Motor
Simulation
Analyze your electric motor design, whether if it is a hairpin motor, a coil motor, an innovative cooling method, or more.
Formula Gearbox
Industrial Gearbox
Automatic Transmission
Leading Engineering Companies Choose Our Simulation Software
.png)
.png)
.png)
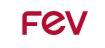

.png)
.png)
.png)
No items found.
Simulate What You Couldn’t Before
Innovative & Reliable
Empower Your Engineering Projects with Dive's Advanced Simulation Tool
Discover the Perfect Fit for Your Industry Needs.
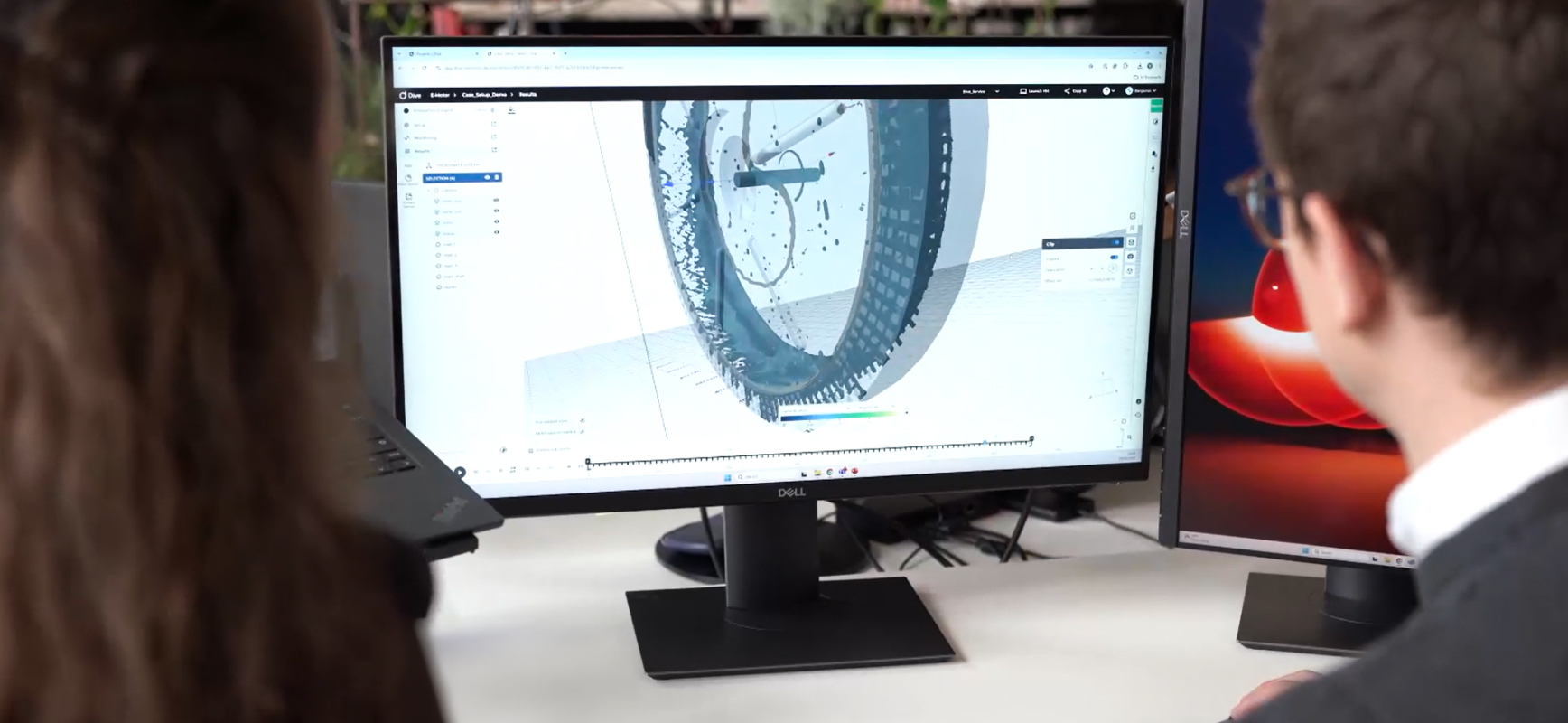
Trusted by Engineering Organizations of All Sizes
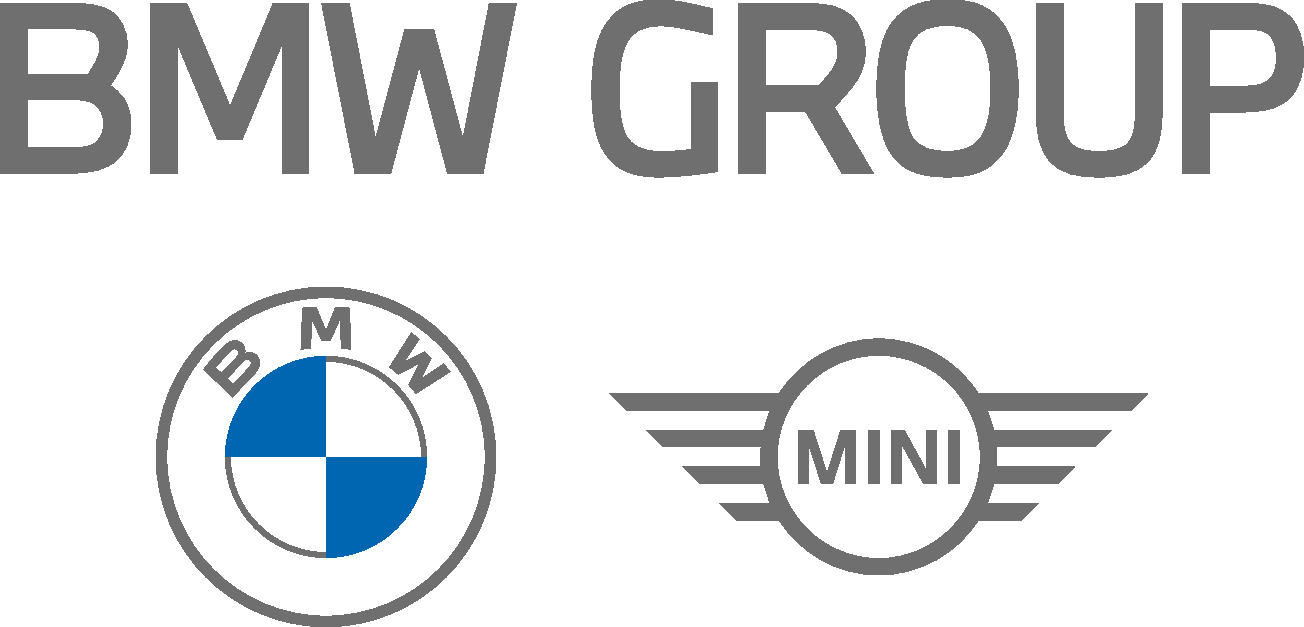
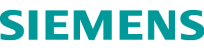
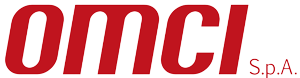
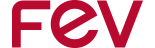
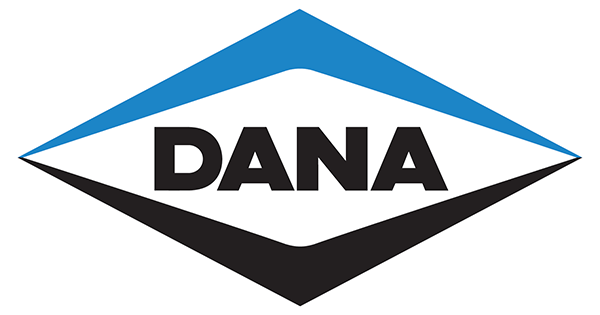
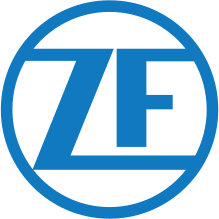

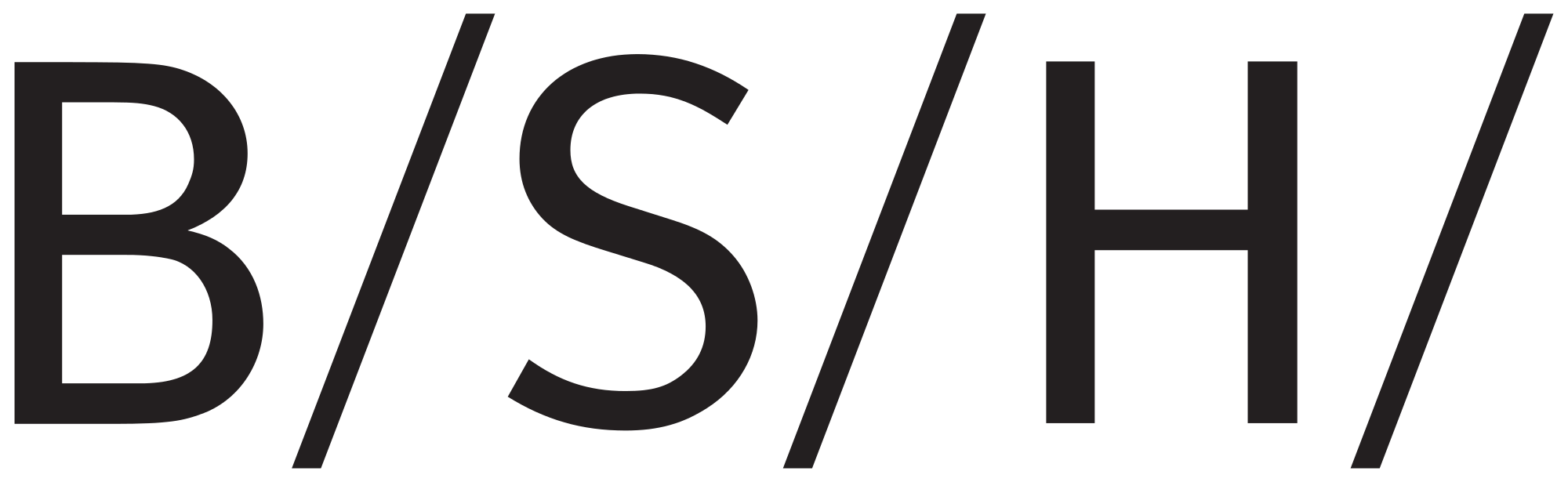
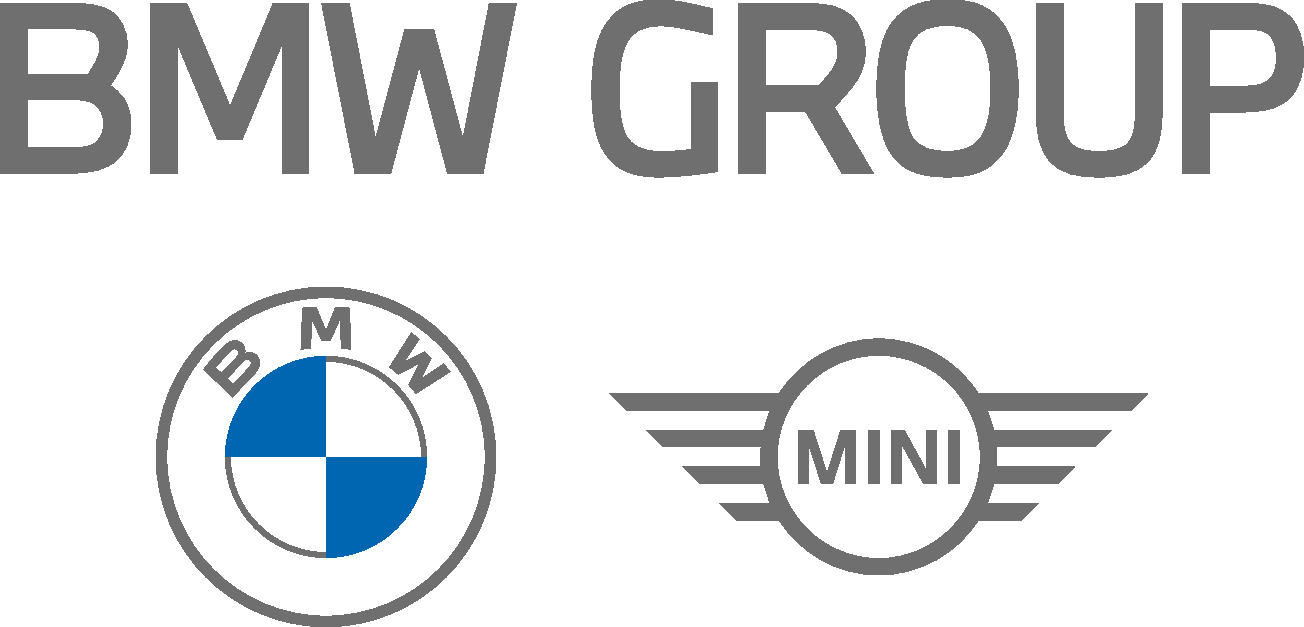
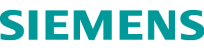
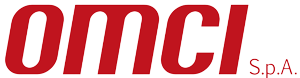
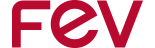
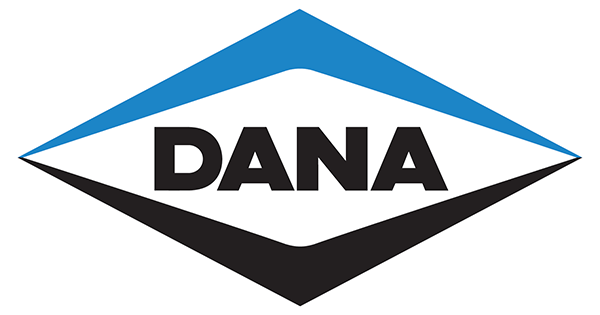
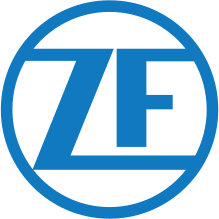

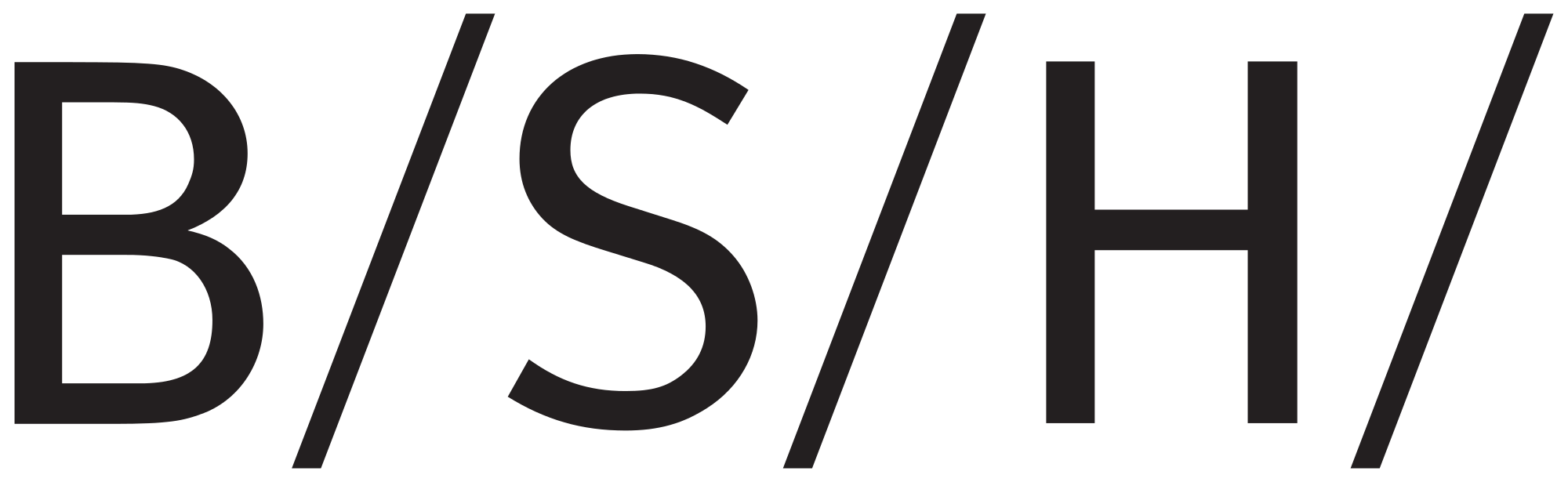
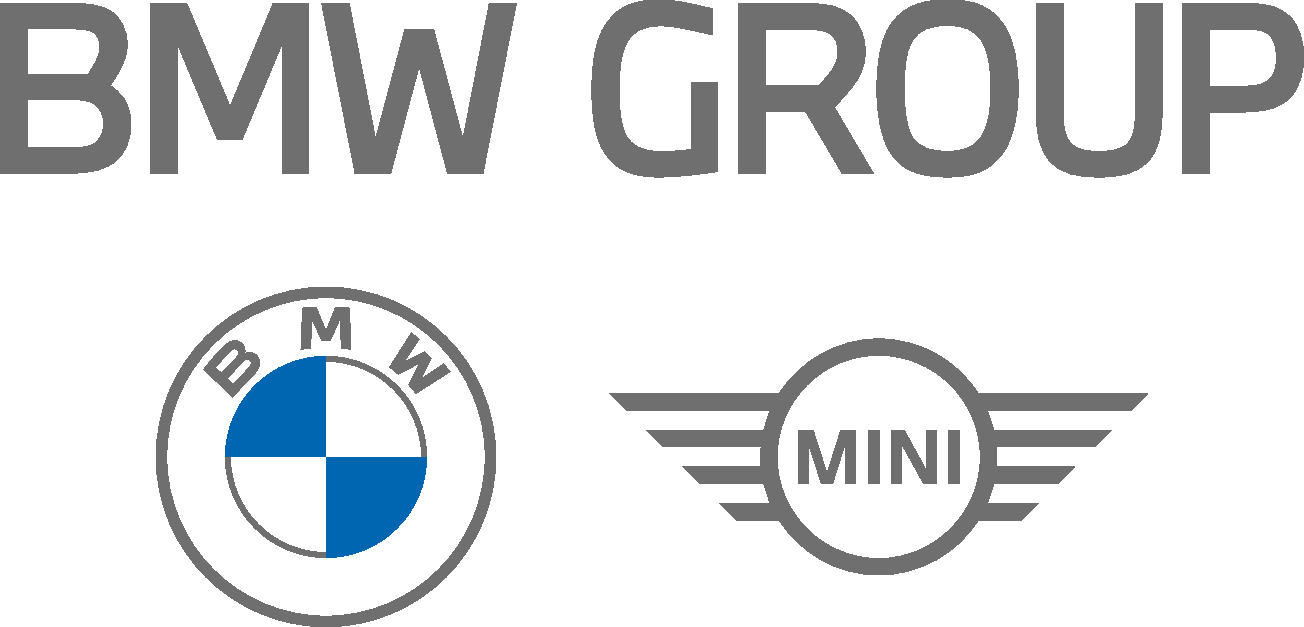
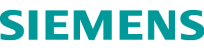
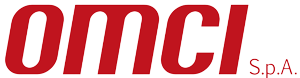
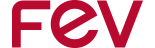
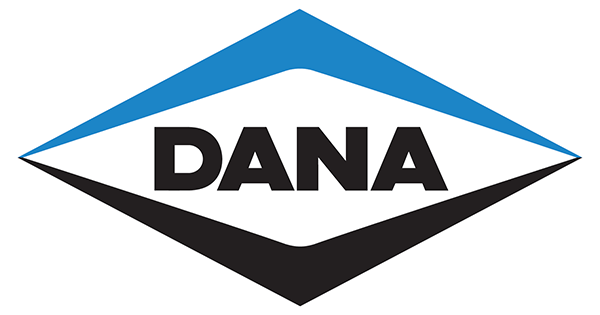
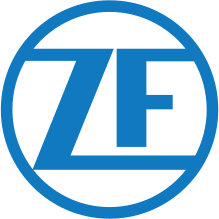

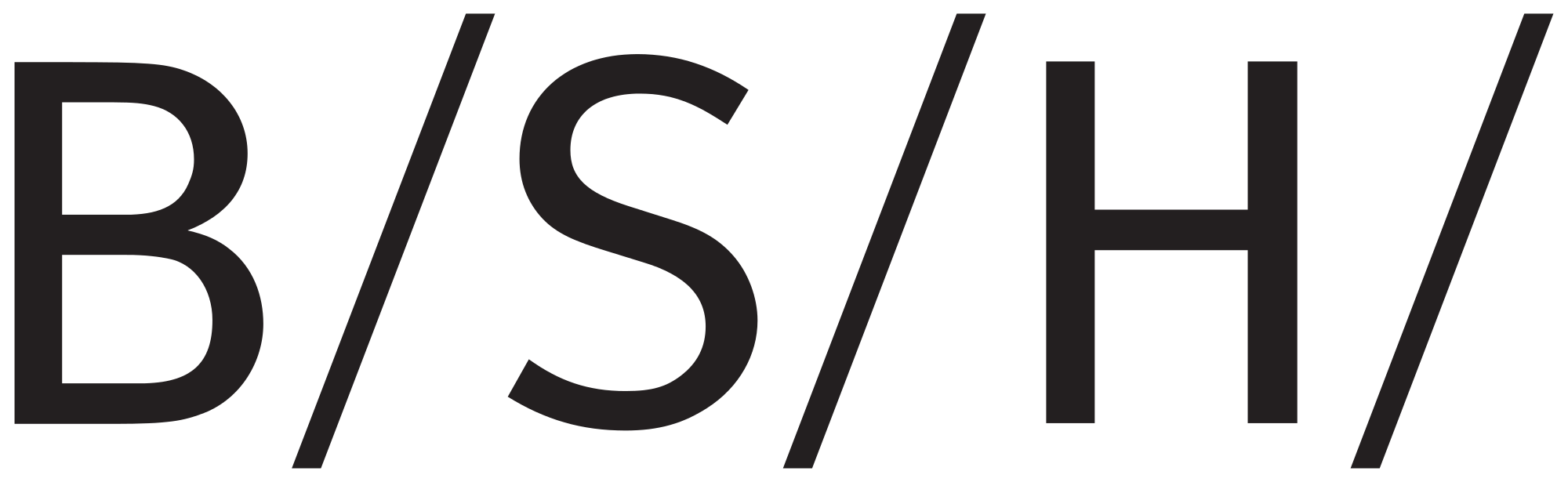
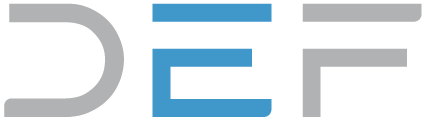
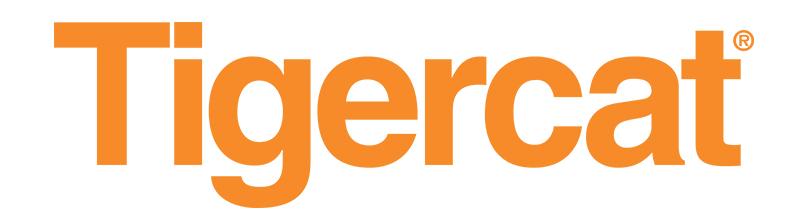
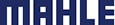
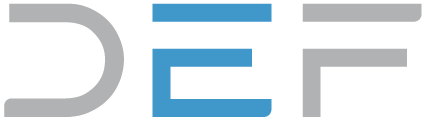
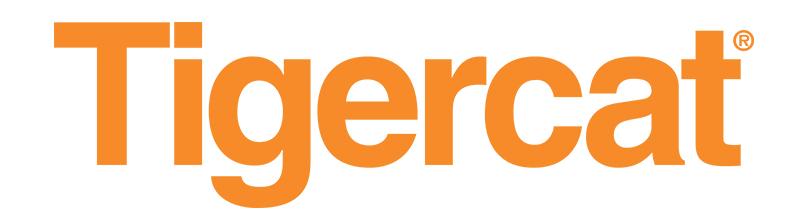
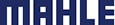
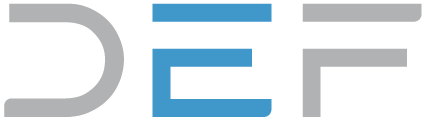
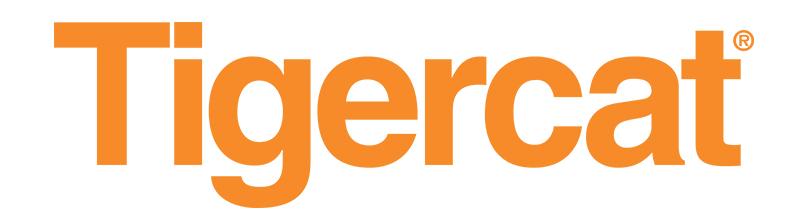
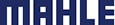